Praca zdalna w sektorze przemysłowym może mieć zastosowanie? Zdalny monitoring stanu urządzeń produkcyjnych, serwisowanie maszyn na odległość? To możliwe. W dobie Przemysłu 4.0. coraz więcej zakładów produkcyjnych korzysta z nowych technologii. W związku z tym wyraźnie redukuje w poszczególnych branżach przestój i straty związane z walką z epidemią.
Według danych Organizacji Współpracy Gospodarczej i Rozwoju (OECD) dotychczas aż sześciu na dziesięciu obywateli Unii Europejskiej nigdy nie przepracowało zdalnie ani jednego dnia. Takie wnioski można było wysnuć z raportów opracowanych w 2019 roku za rok poprzedzający. Specjaliści ze światowej agencji Bloomberg już szacują, że pandemia koronawirusa zrewiduje te wyniki o połowę. Z bieżących analiz wynika bowiem, że współczynnik ten w ostatnich tygodniach zmalał z 60 do około 30%. Podsumowując: ludzie masowo zaczęli pracować z domu – praca zdalna dotyczy głównie pracowników biurowych.
Inteligentne technologie
Dane Eurostatu pokazują, że blisko 65% firm zatrudniających więcej niż 10 osób zapewnia swoim pracownikom odpowiednie warunki techniczne do wykonywania swoich obowiązków z dala od miejsca zatrudnienia. Z pomocą przychodzą nowoczesne technologie: urządzenia mobilne, laptopy, tablety jak i elastyczne oprogramowanie umożliwiające bieżącą komunikację.
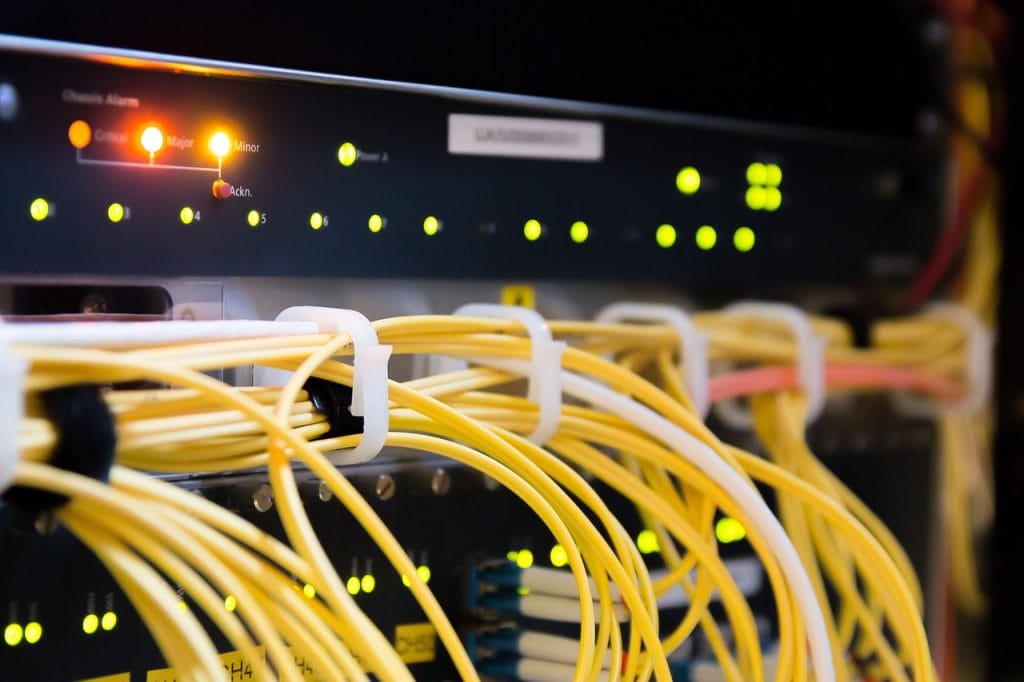
Ekonomiści z agencji Bloomberg w marcu wyliczyli, że przejście na pracę zdalną prawdopodobnie nie będzie realne dla około 17% zatrudnionych. Szczególnie w przemyśle wytwórczym, 14% z branży handlowej, 7% pracujących w budownictwie i 5% osób zrekrutowanych do obsługi hoteli i restauracji. Jednak i te gałęzie mają w tej dziedzinie spory potencjał do wykorzystania. Zwłaszcza w przemyśle zakłady produkcyjne coraz śmielej wdrażają rozwiązania pozwalające na zdalne zarządzanie wieloma procesami oraz zadaniami.
Praca zdalna – przemysł rozwiązań
Współczesny Przemysł 4.0. daje przedsiębiorcom znacznie większą gamę rozwiązań i ochrony w sytuacjach kryzysowych niż miało to miejsce jeszcze kilkanaście lat temu. Zdalna łączność sieciowa i komunikacja istotna jest zwłaszcza w kontekście przemysłu wytwórczego.
– Przejrzystość, wydajność i łączność to słowa kluczowe w optymalizacji, redukcji kosztów i monitorowaniu procesów produkcyjnych. Warunkiem jest ciągła komunikacja, od najmniejszego urządzenia, na przykład w postaci zainstalowanych czujników, poprzez kompletne linie produkcyjne, po całe hale fabryczne i koncerny. Dlatego każdy przestój w produkcji należy pożytecznie wykorzystać. Chociażby na realizację długofalowych potrzeb w procesach technologicznych czy parkach maszyn – mówi Aleksandra Banaś, prezes zarządu katowickiej spółki ifm electronic, produkującej innowacyjne i specjalistyczne czujniki, z których korzysta wiele branżowych zakładów.
Specjaliści jasno podkreślają, że przestoje w zakładach produkcyjnych to idealna okazja do przeprowadzenia niezbędnych prac serwisowych i naprawy parku maszynowego. Taka operacja przyniesie konkretne korzyści i zyski w postaci oszczędności kosztów nawet rzędu kilkudziesięciu procent. Ale przede wszystkim zapewnia optymalizację liczby zatrudnionych w danym przedsiębiorstwie pracowników. Praca zdalna to także między innymi ciągły monitoring stanu maszyn i urządzeń. Prezentacja wartości granicznych i ocena procesów, zbieranie danych podstawowych i wyższego poziomu. Ponadto analiza trendów ciśnienia, przepływu, temperatury, prędkości czy poboru prądu.
Gotowe systemy
Raporty Eurostatu sygnalizują, że co druga firma na Starym Kontynencie, zatrudniająca powyżej 10 osób, byłaby w stanie zdalnie prowadzić procesy. Szczególnie takie, jak: automatyzacja, inwentaryzacja, modernizacja, przeglądy czy serwisowanie. Według analityków wdrożenie tych zastosowań mogłoby spowodować przyspieszenie tych procesów nawet o 40%. Ponadto skutkowałoby zmniejszeniem liczby pracowników zaangażowanych w usuwanie usterek bądź awarii o ponad połowę. Na dokładne dane w tym aspekcie trzeba jednak jeszcze poczekać. Pewne jest, że istotne są tu rozwiązania systemowe, zapewniające wydajność procesową maszyn oraz monitorowanie stanu, serwisowanie zapobiegawcze czy obsługę serwisową.
– Za pomocą narzędzia LR SMARTOBSERVER można wcześnie wykryć problem i zapobiec kosztownym przestojom w produkcji powodowanym zużyciem sprzętu. Konserwacje i naprawy można planować. W związku z tym czas przestoju zostaje skrócony i unika się kosztownych szkód wtórnych. Zróżnicowane schematy wyświetlania i oceny, również w połączeniu z predefiniowanymi mechanizmami alarmowymi, zapewniają ciągły monitoring i analizę wartości energii. Oceny te stanowią podstawę zoptymalizowanych procesów produkcyjnych pod względem kosztów i oszczędzania zasobów – dodaje Aleksandra Banaś.
Źródło: materiał prasowy